Industrial Fan Solutions for the Glass Industry
The glass industry is characterized by diverse products and processes that include a range of applications. From the stage of melting to molding and
cooling to glass tempering, the glass-making involves different processes and production methods
; which require industrial fans and blowers that withstand high temperatures.
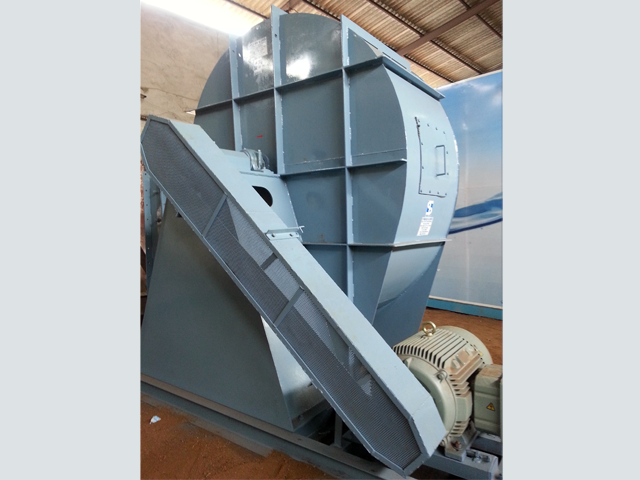
The glass-making process uses a wide variety of fans ranging from ventilation systems to heavy-duty abrasion-resistant fan solutions. Out of which some of the most preferred industrial fans and blowers used to carry out various processes of glassmaking are mentioned below.
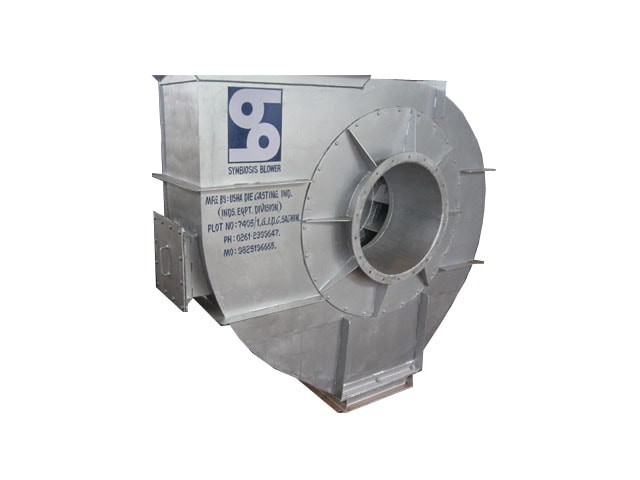
Melting in a furnace:
The glass melting operation uses a wide variety of recirculation fans– i.e. combustion air and furnace fans to draw air through the furnace’s combustion passageway to promote a more efficient running of the combustion, and to allow thorough heat transfer. The melting process uses the Combustion blowers to supply air for efficient burning of fuel and maintain furnace pressure and exhaust waste gas to the atmosphere. Careful selection of industrial fans and blowers for melting operation helps to extend the life of the furnace.
Molten Glass Separation:
At this stage, the molten glass is removed from the furnace, cooled to a uniform temperature, and cut into “gobs” to form glass containers. The molten glass is directed to float on sheet glass forming areas that require exhaust and energy recovery systems. Fiberglass operations direct the molten glass to form sections where large fans pull the glass fibers down onto conveyors. From this point, the fiberglass is treated with resin and binders and baked in large ovens with recirculation fans. Dust control, trim systems, and odor control all use heavy-duty and abrasion-resistant fans.
Glass Tempering:
After thermal heating (furnace), the glass is tempered through quick cooling. Tempered glass or safety glass is usually about four times stronger than ordinary or annealed glass. It is produced by controlling the temperature (extreme heat and quick cooling) of the glass.
Prior to the tempering process, the glass typically is cut to size. The glass is then fed through a heat-treat process in which it passes through a tempering oven that heats the glass to approximately 1200°F (649°C). High-velocity air hits the glass from above and below as it leaves the Lehr furnace. The air rapidly cools and tempers the glass by setting boundary layers in the glass. The glass then undergoes a rapid, high-pressure cooling process called ‘quenching’. This process lasts for only a few seconds.
The tempering process requires significantly high airflow pressures to effectively cool the glass in a short period of time. Industrial fans and blowers for glass tempering provide a
specific cold airflow uniformly blown to cool and temper float or curved
glass, after high-temperature exposition in the furnace. During glass tempering, Backward Curved High-Efficiency Centrifugal fans play a key role in the cooling process. The quantity and the required air pressure depend on the thickness. Unique designs and characteristics of centrifugal fans are a critical component of the cooling process on a tempering system. Accuracy in the fan selection is important for the successful function of this setup.
Once the initial tempering process is completed, the tempered glass continues through an additional cooling process. This subsequent stage requires another centrifugal fan. Overall, the glass-tempering process is unusual in the process cooling arena. At the same time, it is just one more way in which industrial fans are being used for increased manufacturing accomplishments.
Glass casting:
Furnaces are essential for the manufacturing process of glass bottles, jars for oil, wine and spirits bottles, and food vases; which require proper cooling after their production. Gas-fired furnaces require a continuous supply of combustion air for the furnace’s kiln during molding.
Hence the furnace must be equipped with adequate cooling and combustion equipment, while exhausts and fresh air must be provided for worker comfort. Heavy-duty abrasion-resistant fans are typically needed for dust control applications.
Cooling:
Process cooling is the function of removing heat in order to control or maintain appropriate temperature levels. Almost every manufacturing process produces a certain amount of excess heat due to friction or process heating. Hence, process air is required to generate the pressure and airflow necessary to decrease or maintain the proper temperatures.
Glass manufacturers use a variety of Centrifugal fans in heat reduction applications to blow cold air for cooling the industrial material. Fans – both axial and centrifugal, are the primary media to provide such critical pressure and airflow; required for proper process cooling in glass manufacturing.
When liquid glass is distributed from the ovens into different moulds, such as in bottle production, high-pressure fans are installed for mould cooling.
For instance, heavy-duty centrifugal fans find a wide range of applications in the glass industry to cool the oven walls and reduce the temperature of glass material. Likewise, in the case of preparation of flat glass (used in windows), high volume centrifugal fans with medium pressure are often used for cooling. The common centrifugal fans used as cooling fans are airfoil, backward inclined, or high-pressure radial fans.
By offering the most comprehensive line of products, we’ve been able to engineer customized fan solutions for any application in the Glass industry. From the ventilation systems to heavy-duty abrasion-resistant fan solutions, our high-quality fans and blowers are a trusted choice for delivering the right solution to our customers’ specific requirements in the glass industry.
Related Posts
Recent Posts
- Solving Ventilation Challenges in the Ceramic Industry with Symbiosis Blowerfab
- Commercial Kitchen Ventilation Systems: A Complete Guide for Restaurants
- 6 Ways Air Washer Systems Enhance Efficiency in Industrial Processes
- 6 Ways to Ensure Adequate Air Ventilation in Battery Manufacturing Industry
- 4 Ways Industrial Blowers and Fans Enhance Efficiency in Automotive Industry