Industrial Fan Solutions For Cement Industry Applications
From city building development to transportation infrastructure, the Cement industry plays an important role in the structural infrastructure development and in the overall economic growth of the country. It is a highly energy-intensive industry, in which the correct airflow systems are crucial for optimum production and profitability.
Cement manufacturing requires Specific industrial fans to efficiently handle and manage various processes of moving, grinding, preheating to heating, and cooling. Plus efficient Air filtration systems become a critical part to ensure the cement manufacturing plant meets strict environmental regulatory requirements. Therefore Cement manufacturers utilize different industrial fans in the cement manufacturing process at various steps such as material handling, preheating, cooling, etc.
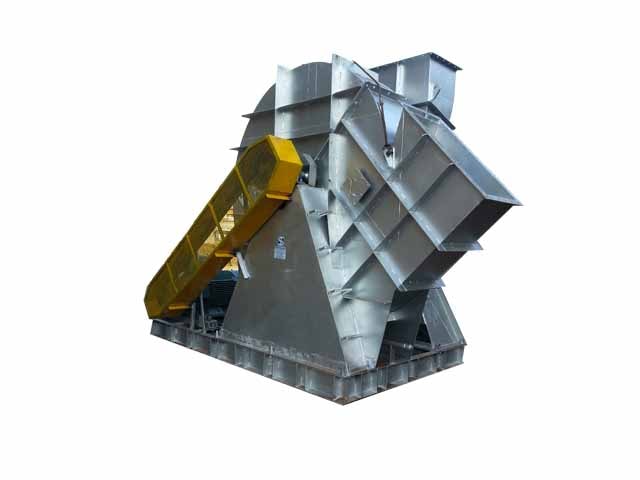
Fans employed in cement manufacturing are heavy-duty. They perform two basic functions i.e. supply of air or removal of exhaust gases and material handling. Variety of process fans that find applications in the cement industry are – raw mill fans, induced draft fans, cooling fans, raw mill exhaust fans, coal mill fans, and cooler exhaust fans. The heater is used in industrial dry kiln cement production plants to heat the raw mix and drive out carbon dioxide & water before it is fed into the kiln.
Both Centrifugal and Axial Fans are useful in the cement production line as per their own typical complexities. (i.e. notable dimensions, high temperatures, accumulation of dust, the abrasiveness of the fluid, and the need for a high output solution). Industrial fans and blowers required by the Specific process, systems, and related applications in the Cement Industry are listed below.
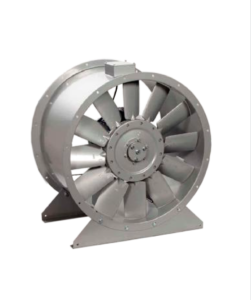
Induced Draft Fans:
Induced draft fans are used in the kiln of cement to supply necessary air for the combustion of fuel. ID fans are applied to generate a negative pressure airflow to guarantee the proper work for a dust abatement system in a filtration device. ID Fans used in cement production are radial, forward-curved, or backward inclined centrifugal fans. If these induced fans are not manufactured and operated properly, it may affect the power consumption of the cement factory.
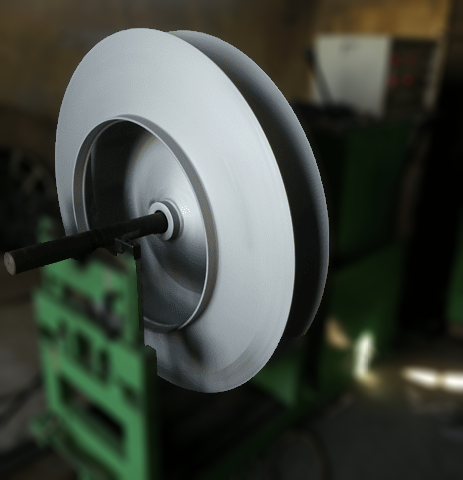
Coal Mill Fans:
In the cement industry coal mill fans are used to supply the required air for burning coal and remove the exhaust gases produced after burning. This is where the coal is grinded into the proper size to be fed into the burner. The coal mill fan moves the coal into the grinder. Thus these fans help ineffective burning of coal inside the mill.
Cooling Fans:
Cement manufacturers use a large number of cooling fans to blow cold air to the cooler and to cool the clinker from 1500oC to 100oC. Usually, 5 to 15 cooling fans are used in each clinker line depending on the plant’s kiln capacity. Cooling kiln protects equipment and facilitates quenching the clinker, to ensure the important forms of minerals like C3S, C2S, C3A, C4AF stay in it. Appropriate design of cooling fans is essential for –
- Maintaining the quality of clinker and conveying system
- Curtailing the power consumption in a cement manufacturing plant.
It is recommended that the cooling fans be provided with variable speed drives to obtain the benefit of lowering the cooling air requirement.
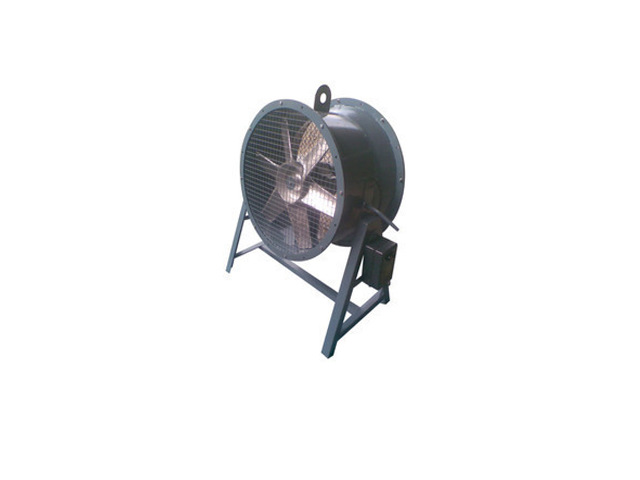
Raw Mill Fans:
Raw mill fan is used in a cement factory to carry gas and raw meal. The raw mill fan is of large capacity and its specifications are determined by the mill characteristics. If a vertical roller mill is used for raw grinding in the cement industry then a large raw mill fan is installed. Usually, cement manufacturers prefer centrifugal fans to carry out this process.
Dust collector fans:
Dust Collector fans are the main equipment of dust removal systems in cement plants. They offer the power source to the whole system and overcome the resistance loss caused by the airflow in the system.
Raw Mill Exhaust Fans
Raw mill exhaust fans/ stack fans also known as de-dusting fans handle 2.2 tons of exhaust gases for the production of 1 ton of clinker. Raw mill exhaust fans are operated in a cement factory with very adverse situations because these fans mostly handle gases like CO2, N2, NOx, and Sox along with some dust particles.
Clinker cooler:
Cooling fans & clinker cooler exhaust fans circulate fresh air to the clinker to cool down the material. Cooler exhaust fans move 1.8 tons of exhaust air per 1 ton of clinker production. This process is a part of air blown into the cooler by cooling fans that are not useful for fuel combustion.
In addition to these key process fans, the cement industry also utilizes many non-process fans. These fans work in tandem with bag filters, for the de-dusting of various conveying systems.
From the large combustion air and kiln fans to the smallest air slide blowers; Usha Die Casting Industries is able to engineer individual, customized solutions for any application in the Cement manufacturing industry. UDCI’s sophisticated range of fans & blowers is field-proven to perform optimally in challenging operating environments. SYMBIOSIS fans and blowers are the trusted choice in a number of key vertical markets, while also covering a wide spectrum of specific requirements for a variety of niche businesses.
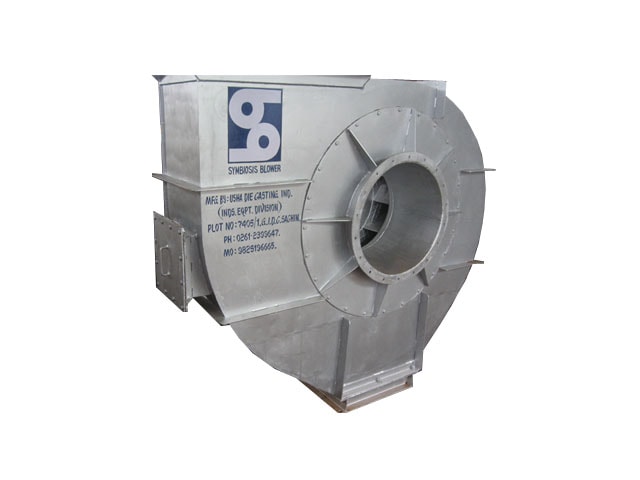
Choosing Industrial fans with appropriate characteristics for different applications is critical; as the requirement may vary with the individual configuration of the plants. Contact our experts to understand the fan requirement for your Cement Manufacturing capacity.
Recent Posts
- Solving Ventilation Challenges in the Ceramic Industry with Symbiosis Blowerfab
- Commercial Kitchen Ventilation Systems: A Complete Guide for Restaurants
- 6 Ways Air Washer Systems Enhance Efficiency in Industrial Processes
- 6 Ways to Ensure Adequate Air Ventilation in Battery Manufacturing Industry
- 4 Ways Industrial Blowers and Fans Enhance Efficiency in Automotive Industry